TECHNOLOGY
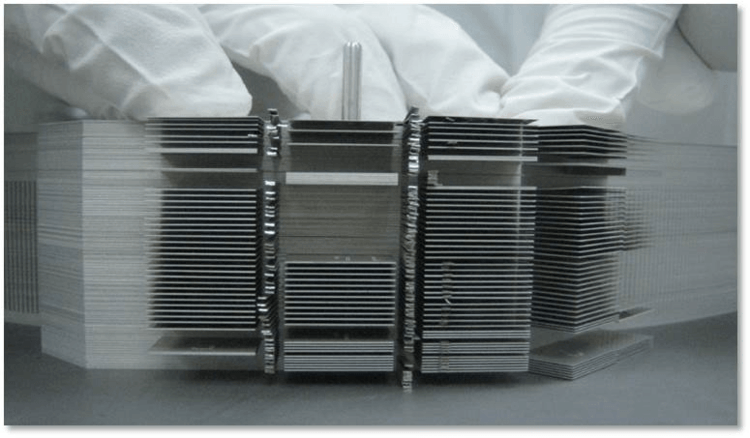
Overview
The compact platelet heat exchanger (CPHX) utilizes platelet technology. This highly mature manufacturing technique was first developed by Aerojet, an American rocket and missile propulsion company, in the mid-1960s. The resulting process allows the fabrication of monolithic structures containing complex and precise, 3D flow passages and features. Built effectively layer by layer, these diffusion bonded heat exchangers possess the unique ability to control and maintain stable combustion in rocket engines while maintaining cool metal temperatures in proximity to 3,300°C flame fronts. Applying this technology from the aerospace industry to thermal management devices such as heat exchangers was a natural transition.
Platelet Technology
Platelet technology provides solutions to difficult thermal and fluid flow problems across a variety of market applications. The process begins with thin sheets of metal that are photo-chemically etched to specific design patterns to produce "platelets." Individual platelets are then accurately assembled, or "stacked," and joined via a diffusion bonding process. The result is a monolithic structure containing complex internal passages that allow for precise flow control, fluid manifolding and metering features. Also, in-situ filters can be included to preclude plugging or occlusion. The diffusion bonding process effectively seals the passages between the fluid circuits with a solid metal barrier, isolating and segregating flows. This allows for much higher operating pressures and temperatures than achievable with traditional heat exchangers.
Diffusion Bonding
Diffusion bonding is a solid state process, i.e. no melting takes place, that produces a monolithic joint through the formation of bonds at the atomic level. After the platelets are stacked, they are heated and compressed in a vacuum hot-press bond furnace under precisely controlled conditions. The mating surfaces of the platelets are forced into intimate contact due to local plastic deformation at elevated temperatures; elemental diffusion across the platelet interface begins, along with grain boundary migration. At the completion of the process, all surface layers of the platelets are joined through inter-diffusion and the original interfaces and boundaries are fully coalesced, creating a singular device. When performed with HEXCES developed parameters, no macro-scale deformation occurs during the bonding process, leaving the as-fabricated platelet features intact with parent material strength. These assemblies cannot be fabricated by any other current conventional or unconventional process.
Historical Platelet Devices
The first CPHX was developed by Aerojet engineers under an independent research and development (IR&D) program in the mid-1970s. This compact lightweight heat exchanger used platelet technology to heat cold, high pressure liquid hydrogen with warm low pressure gaseous hydrogen for rocket applications.
Perhaps the most famous application of the platelet technology employed by HEXCES personnel is the two-fluid, oxidizer/fuel injector of the NASA Space Shuttle Orbital Maneuvering System Engine. This rocket engine exhibited a spotless 100% reliability record over the 30 year lifespan of the Space Shuttle program, which included extensive cycling in the extreme environments of outer space.
Another example from the Space Shuttle program is a heat exchanger for the Shuttle’s main engine. This CPHX, designed for the autogenous oxygen pressurization system, solved a catastrophic failure mode with a robust, light weight, dual material, multi-circuit design. An evolution of the first CPHX and made from a combination of stainless steel and copper alloys, this exchanger is capable of operating at pressures in excess of 275 bar with both liquid and gaseous fluid streams.
HEXCES heat exchangers and systems are a product of the world's foremost platelet experts. We continue to lead the way with innovative designs for thermal fluid management systems, able to withstand the most difficult of operating conditions.